机械设备超声波探伤检测
金属表面检测的应用领域和范围有哪些?1、金属制造业:金属制造业中的各种金属制品的生产过程中,需要进行金属表面检测,确保其表面无缺陷,达到质量要求。2、机械制造:机械制造业中各种零部件的生产过程中,需要进行金属表面检测,保证其表面清洁、无缺陷,以保证机器运行的安全和可靠性。3、航空航天:在航空航天领域,需要对各种金属材料进行表面检测,以确保其机械性能和表面状态符合航空航天的要求。4、汽车制造:汽车制造行业需要对各种汽车零部件的金属表面进行检测,以确保其机械性能和表面状态符合汽车行业的要求。检测环境严格控制,保障数据精确度。机械设备超声波探伤检测
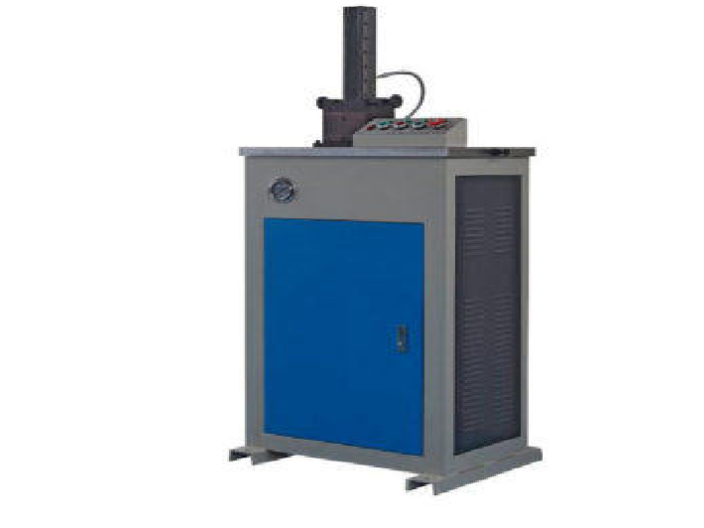
非破坏性金属材料检测的优点是什么?1、保护被检测材料:在进行非破坏性金属材料检测时,不需要对被检测材料进行损伤,可以有效保护金属材料的完整性和使用价值。2、高效检测:非破坏性金属材料检测可以快速地对大量金属材料进行一次性检测,可显著提高生产效率,减少工作量。3、提高精度和可靠性:非破坏性金属材料检测通过多种科学检测方法,可以得出更准确的检测结果,相对于传统的破坏性检测方法,检测结果更加可靠。4、节约成本:非破坏性金属材料检测不需要重新加工或更换被检测材料,可以有效地降低生产成本。成都金属板材热处理检测严格遵循行业标准,确保检测公正性。
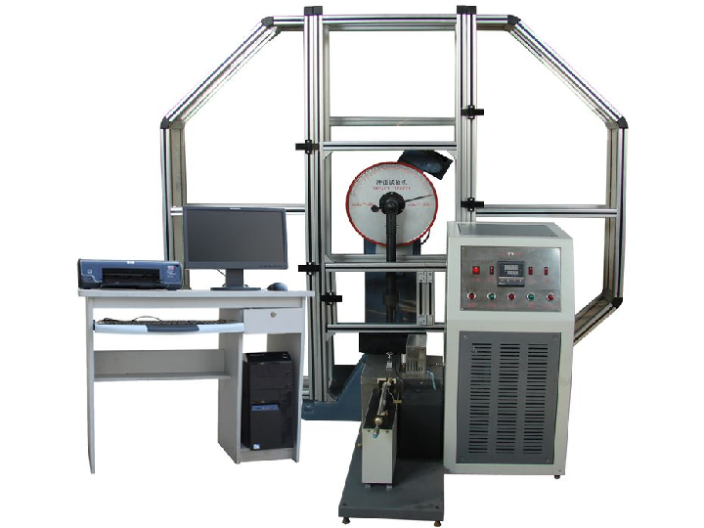
金属材料检测在制造业中的重要性在制造业的广阔版图中,金属材料检测如同一座坚实的桥梁,连接着原材料与**终产品,其重要性不言而喻。首先,从质量控制的角度来看,金属材料检测是确保产品质量的***道防线。通过严格的检测流程,可以及时发现并剔除存在缺陷或不符合标准的材料,防止其流入生产线,从而避免生产出次品或废品,减少企业的经济损失和品牌风险。其次,金属材料检测对于产品性能的稳定性至关重要。金属材料的性能直接决定了产品的使用寿命、安全性以及可靠性。通过检测,可以***了解材料的力学性能、耐腐蚀性能、抗疲劳性能等关键指标,为产品的设计、制造和使用提供科学依据,确保产品在不同工况下都能保持稳定的性能表现。此外,金属材料检测还有助于推动制造业的技术创新和产业升级。在检测过程中,企业可以积累大量的数据和经验,为新材料的研发、旧材料的改良以及生产工艺的优化提供有力支持。这些成果不仅可以提升企业的核心竞争力,还能推动整个行业的技术进步和可持续发展。综上,金属材料检测在制造业中具有举足轻重的地位。它不仅是确保产品质量、保障消费者安全的必要手段,也是推动行业技术创新、实现产业升级的重要途径。
金属无损探伤测试的应用领域有哪些?1、航空航天领域:对飞行器、发动机、燃气轮机等关键部件进行无损检测,确保其安全性和可靠性。2、石化、电力、核电及化工等行业:对管道、储罐、压力容器等设备进行缺陷检测,保障设备安全运行。3、汽车制造和维修:对汽车发动机、变速器、轮轴等关键部件进行无损检测,确保汽车的安全和性能。4、金属材料加工和制造业:对钢铁、铝合金、铜合金等金属材料进行无损检测,确保材料质量,预防材料缺陷。5、建筑、桥梁、隧道等公共工程建设:对构件材料进行无损检测,保障项目的安全和质量。报告数据详实,为企业决策提供依据。
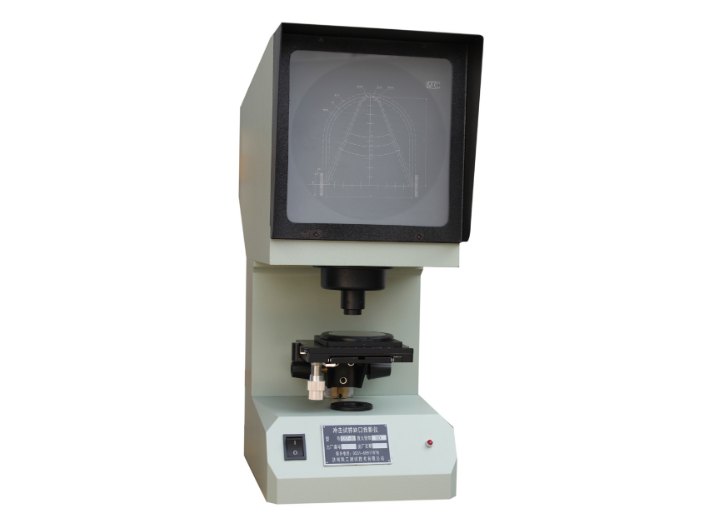
金属金相分析的显微镜观察条件是什么?1、光源:使用透射式光源,如白炽灯或LED灯。2、显微镜的调焦:使用高精度的调焦机构,以便观察样品表面和内部的细节。3、样品制备:样品必须被切割、研磨和抛光,以获得平滑的表面。4、样品染色:染色可以增强样品的对比度,使细节更加清晰。5、显微镜的对比度调节:可以通过调节显微镜的对比度,使细节更加清晰。6、显微镜的亮度调节:可以通过调节显微镜的亮度,使细节更加明显。7、显微镜的颜色调节:可以通过调节显微镜的颜色,使细节更加明显。定制检测方案,满足不同金属材料需求。成都金属板材热处理检测
检测环境不断优化,提升检测服务水平。机械设备超声波探伤检测
韧性评估,作为机械零件抵抗断裂能力的重要衡量标准,是机械性能检测中不可或缺的一环。它关注的是材料在受到冲击或突然载荷时,吸收能量并抵抗断裂的能力。韧性好的零件,在面对复杂多变的工况时,能够更有效地抵御裂纹的萌生和扩展,从而延长使用寿命,确保设备的安全稳定运行。韧性评估通常通过冲击试验来实现,该试验模拟了零件在实际工作中可能遭遇的突然冲击载荷。在试验中,观察并记录零件在受到冲击后的变形情况、断裂形态以及吸收的能量,从而评估其韧性水平。此外,还可以通过断裂力学分析等方法,进一步探究材料的断裂机制,为优化材料配方、改进零件设计提供科学依据。综上所述,韧性评估对于提升机械零件的性能和可靠性具有重要意义。通过科学的评估方法,可以准确判断零件的韧性水平,为产品的质量控制和性能优化提供有力支持。机械设备超声波探伤检测
上一篇: 江苏金属外观检测
下一篇: 金属管材精密尺寸测量大概多少钱