机械零部件无损探伤测试售价
金属材料检测是一种对金属材料进行质量检查的方法。金属材料在制造、加工、运输过程中可能会出现缺陷、损伤或不均匀性等问题,这些问题可能会影响金属材料的性能和寿命,甚至危及人的安全。因此,金属材料检测是至关重要的。金属材料检测的目的是评估金属材料的性能和组成,以确定其是否符合特定的质量标准、安全标准或性能要求。这些测试可能包括非破坏性测试(NDT)和破坏性测试(DT)。非破坏性测试技术可以检测金属中的缺陷、损伤或不均匀性,而不会对金属造成破坏;破坏性测试则通常是将样品置于极端条件下进行测试,以评估其性能和强度。工序检测细致入微,不放过任何潜在问题。机械零部件无损探伤测试售价
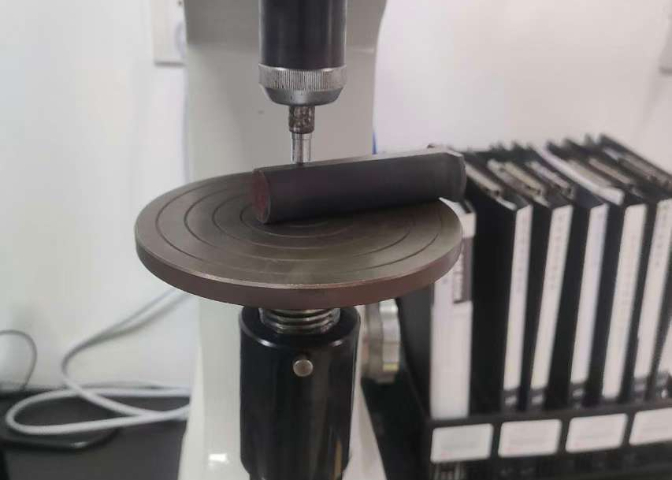
深度解析机械性能检测标准与流程,是确保检测工作科学、规范、有效的基石。首先,机械性能检测标准通常由国际或行业**机构制定,明确了检测项目的具体要求、方法、设备及精度等,旨在保证检测结果的统一性和可比性。这些标准涵盖了材料的拉伸强度、屈服强度、硬度、冲击韧性、疲劳寿命等多个方面,为检测工作提供了明确的指导。流程方面,机械性能检测通常包括样品准备、预处理、测试执行、数据记录与分析以及报告编制等步骤。样品准备需确保代表性,预处理则可能包括热处理、去应力等过程以消除外部干扰。测试执行时,需严格按照标准操作,确保数据的准确性和可靠性。数据记录与分析是**环节,通过对比标准值,评估材料的性能优劣。***,编制详尽的检测报告,总结检测结果,提出改进建议。综上所述,机械性能检测标准与流程的严谨执行,对于保障设备安全、提升产品质量具有重要意义。广州机械零部件金相分析检测报告清晰明了,方便企业质量管理。
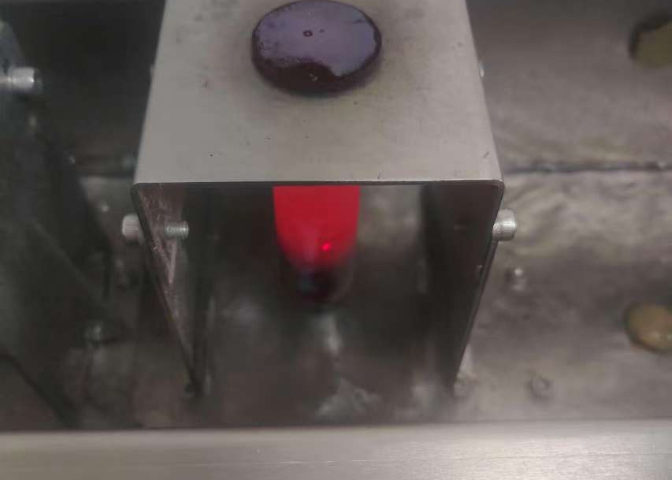
金属金相分析的显微镜观察条件是什么?1、光源:使用透射式光源,如白炽灯或LED灯。2、显微镜的调焦:使用高精度的调焦机构,以便观察样品表面和内部的细节。3、样品制备:样品必须被切割、研磨和抛光,以获得平滑的表面。4、样品染色:染色可以增强样品的对比度,使细节更加清晰。5、显微镜的对比度调节:可以通过调节显微镜的对比度,使细节更加清晰。6、显微镜的亮度调节:可以通过调节显微镜的亮度,使细节更加明显。7、显微镜的颜色调节:可以通过调节显微镜的颜色,使细节更加明显。
金属金相分析的样品制备步骤是什么?1、样品的选择:选择与研究对象相符合的样品进行分析研究。2、样品的切割:用钢锯或切割机将样品切割成所需的尺寸和形状。3、样品的打磨:用不同粒度和不同材料的砂纸和抛光布进行逐级打磨,直到样品表面光滑洁净。4、样品的腐蚀:一些金属样品的组织和结构不易通过直接观察进行分析,需要将其进行腐蚀处理。将制备好的样品用有机或无机酸进行腐蚀,直至获得所需的组织和结构。5、样品的彩色化处理:彩色金相试样是用化学方法使试样表面染上不同颜色而制成的样品,用以观察金属的组织结构、颗粒尺寸和相状态等特征。彩色金相试样的制备包括腐蚀、漂白、染色、水洗和抛光等多个步骤,各步骤精细的操作对彩色化处理效果均有影响。检测机构信誉良好,服务质量有保障。
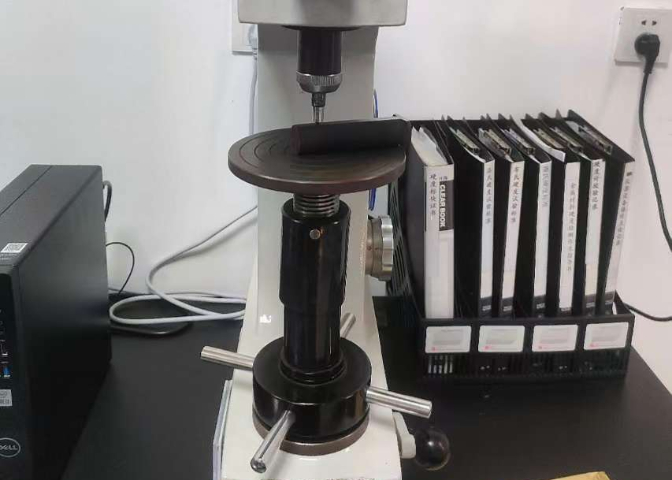
前沿趋势:智能化金属材料检测系统的发展与挑战随着人工智能、大数据等技术的飞速发展,智能化金属材料检测系统正逐步成为行业前沿趋势。这一系统通过集成先进的传感器、数据处理算法与机器学习模型,实现了对金属材料性能的高效、精细检测。智能化检测系统的发展带来了诸多优势。首先,它能够自动完成检测任务,减少人工干预,提高检测效率与准确性。其次,利用大数据分析技术,系统能深入挖掘检测数据背后的规律与趋势,为材料研发与工艺优化提供有力支持。此外,智能化的预警与诊断功能,还能及时发现潜在问题,预防质量事故的发生。然而,智能化金属材料检测系统的发展也面临着诸多挑战。如何确保检测数据的真实性与可靠性,防止算法偏见与误判;如何保障系统在不同环境下的稳定性与适应性,避免外界因素干扰;以及如何加强数据安全与隐私保护,防止信息泄露与滥用等问题,都需要行业内外共同努力解决。严格遵循行业标准,确保检测公正性。北京金属环境模拟测试
检测标准科学严谨,保障产品质量安全。机械零部件无损探伤测试售价
金属表面检测的方法有哪些?1、目测检测:通过裸眼观察金属表面,检查是否存在表面缺陷,如划痕、氧化等。2、镜面检测:采用一个光滑、平整、反光的表面,将其放置在被测金属表面,以检查金属表面的平整度和物体的变形情况。3、金相显微镜分析:使用金相显微镜观察并分析金属表面组织结构,检查裂纹、晶界、含碳量等变化。4、电子扫描显微镜分析:通过使用电子扫描显微镜来精确观察金属表面或断口区域的形貌、颗粒大小和分布、元素成分等。5、硬度测试:通过在金属表面上进行硬度测试来评估金属表面的硬度和强度,并检查数据是否根据标准规范。机械零部件无损探伤测试售价
上一篇: 杭州金属锻件热处理检测
下一篇: 郑州金属脱碳检验