吉林热处理加工制造厂
等温淬火热处理工艺广泛应用于各种金属材料的热处理,如钢铁、铝合金、钛合金等。它可以显著提高金属材料的强度、硬度、韧性和耐磨性,延长零件的使用寿命。总之,等温淬火热处理工艺是一种先进的金属热处理工艺,它可以显著提高金属材料的性能,延长零件的使用寿命。在实际应用中,需要根据金属材料的特性和零件的使用要求,选择合适的等温淬火工艺参数,以获得比较好的热处理效果。通过等温淬火获得下贝氏体组织,其综合性能良好,即拥有高的疲劳强度和韧性,同时可避免马氏体组织脆性问题,相比常规的钻头工艺生产能多打60-70个眼。建筑材料也可应用热处理加工,提升性能。吉林热处理加工制造厂
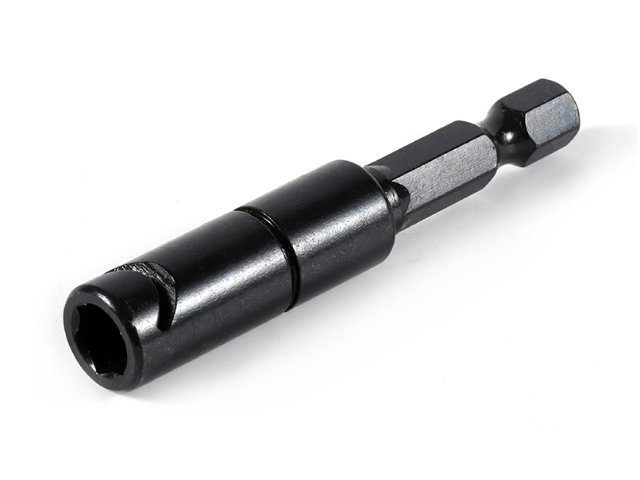
后处理:对热处理后的金属材料进行清洗、干燥和防锈处理,以保护其表面质量。酸洗热处理加工在工业中有着广泛的应用。例如,在钢铁行业中,酸洗热处理可以用于提高钢材的表面质量和耐腐蚀性;在汽车制造中,酸洗热处理可以用于强化汽车零部件的性能;在航空航天领域,酸洗热处理可以用于制造强度高的金属部件。总之,酸洗热处理加工是一种重要的金属加工工艺,它能够提升金属材料的性能和质量,满足不同工业领域的需求。通过合理的酸洗热处理工艺,可以获得具有优异性能的金属材料,为工业生产提供可靠的支持。黑龙江调质热处理加工重视热处理加工,发掘金属材料的无限潜力。
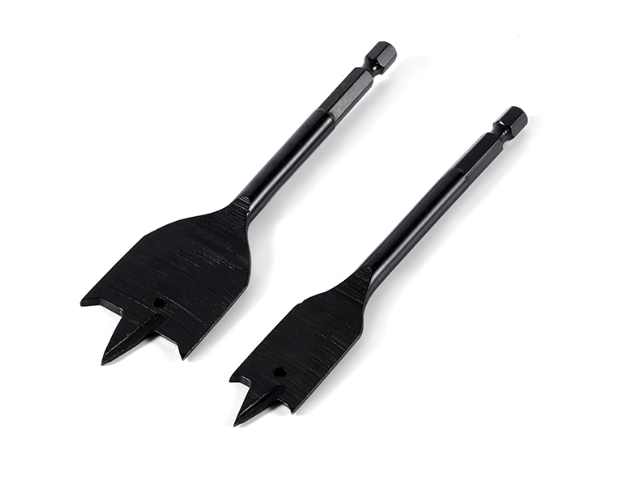
在金属加工领域,回火热处理是一项至关重要的工艺,它能够改善金属材料的性能,使其更加适应各种复杂的工作环境。回火热处理通常在淬火之后进行。淬火是将金属加热到一定温度后迅速冷却,以提高其硬度和强度。然而,淬火后的金属往往存在内应力较大、脆性增加等问题,这时候就需要回火热处理来加以改善。回火热处理的原理是将淬火后的金属重新加热到一定温度,然后以适当的速度冷却。在这个过程中,金属内部的组织结构发生变化,残余应力得到释放,从而降低了金属的脆性,提高了其韧性和塑性。同时,回火还可以使金属的硬度保持在一个较为合适的范围内,既满足了使用要求,又避免了过度硬化带来的脆性问题。回火热处理的温度和时间是影响其效果的关键因素。一般来说,回火温度越高,时间越长,金属的韧性和塑性就越好,但硬度会相应降低。因此,在进行回火热处理时,需要根据金属材料的种类、用途以及对性能的要求等因素,合理选择回火温度和时间。
这一过程中,碱性溶液中的成分和温度都需要严格控制,以确保氧化膜的质量和均匀性。接下来,将金属材料放入中和液中进行中和处理,以去除残留的碱性溶液。,再次进行清洗和保护处理,以保证金属表面的干净和耐腐蚀性。碱性发黑热处理加工的优点主要体现在以下几个方面。首先,通过形成氧化膜,可以提高金属材料的耐腐蚀性。氧化膜具有一定的保护作用,可以防止金属表面被氧化、腐蚀等。其次,碱性发黑热处理加工可以改善金属材料的美观度。热处理加工,为金属材料开启精彩的性能之旅。
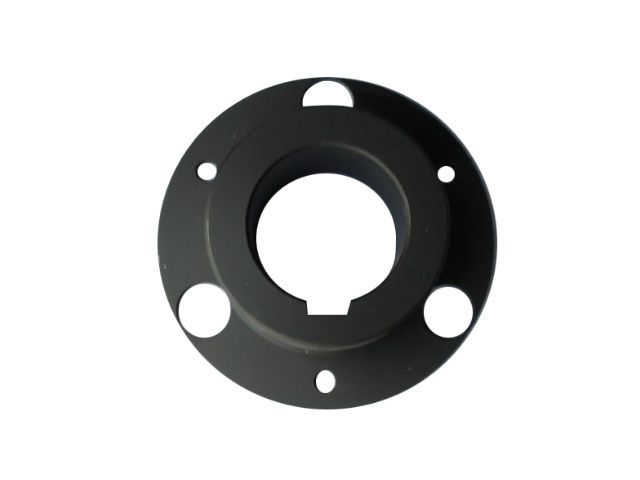
热处理它是一种材料,在固态下通过加热保温或者冷却手段,以获得预期组织和性能的金属加工工艺,在从实际时代进展到铜器时代和铁器时代的过程中,热处理的作用逐渐为人们所知,也就在过年前700多年,中国人就已经生产和实践中发现了钢铁的性能会因温度加热而变形的影响变化,逐渐的就成为了一个比较实用,而且受欢迎的工艺。实际上热处理的分类目前是有几种分类,一般来讲金属热处理工艺大致可分为整体热处理,表面热处理,化学热处理三大类主要是根据介质加热温度和冷却方法不同,每一大类可区分为若干不同热处理工艺,同一种金属采用不同的热处理工艺,可获得不同的组织,从而具有不同的性能,钢铁就是工业上应用普遍的金属,而且钢铁显微组织也比较复杂,因此钢铁热处理工艺种类是比较繁多,一般整体的热处理是对工件整体加热,然后速度冷却的一个过程。热处理加工使金属材料更耐用,广泛应用于工业领域。陕西酸洗热处理加工厂
专业热处理加工,确保产品质量稳定可靠。吉林热处理加工制造厂
等温淬火热处理是一种热门的金属热处理工艺,它通过在特定温度下进行淬火和回火处理,使金属材料获得优异的性能。本文将详细介绍等温淬火热处理工艺的原理、过程和应用。原理等温淬火热处理的原理是基于金属材料的相变特性。在等温淬火过程中,金属材料被加热到一定温度,使其发生相变,形成奥氏体。然后,将金属材料迅速冷却到等温温度,使其在该温度下保持一段时间,使奥氏体转变为贝氏体或马氏体。总之,将金属材料进行回火处理,以去除淬火应力,提高韧性和延展性。过程等温淬火热处理工艺通常包括以下步骤:加热:将金属材料加热到奥氏体化温度,使其完全转变为奥氏体。淬火:将加热后的金属材料迅速冷却到等温温度,使其在该温度下保持一段时间,使奥氏体变为贝氏体或马氏体。回火:将淬火后的金属材料进行回火处理,以去除淬火应力,提高韧性和延展性。吉林热处理加工制造厂
上一篇: 江西热处理加工制造厂
下一篇: 上海工具件热处理加工